Portuguese footwear components focus on sustainability
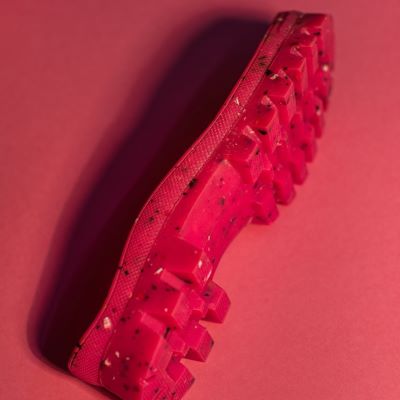
Under the Bioshoes4All project, the Portuguese footwear components industry is investing heavily in the development of a new generation of sustainable products. Meet some of them
At the latest edition of the Lineapelle trade fair in Milan, the Portuguese footwear components industry presented several sustainable solutions developed as part of the Bioshoes4all project, supported by the PRR. “We’re developing highly differentiated and technologically advanced products because we believe that if Portugal wants to be at the forefront, it has to make significant investments to become a major international benchmark”, summed up Paulo Gonçalves, spokesperson of the Portuguese Footwear, Components, Leather Goods Manufacturers’ Association (APICCAPS).
Aloft’s E-Blast attracts foreign investment
E-blast, the gas-expanded polymer produced by Aloft in its Vila Conde factory and developed under the BioShoes4All project, is attracting interest from major international sports footwear brands, which are considering setting up in the country to be closer to the source of their soles.And Aloft itself is transforming as it prepares to take the plunge and produce injected footwear from 2025. It has already taken its first steps in this field by partnering with Decathlon, a multinational company with which it has developed “the world’s first sneakers made entirely without the use of any type of glue”. The ambition is to move from soles to manufacture highly technical sports products.
The first E-Blast soles, an innovative technology presented by Aloft at the September edition of Lineapelle, are now being produced 24 hours a day, seven days a week. The result is ultra-light, sustainable soles with reduced labour requirements, a product that Pedro Castro, Aloft’s CEO, hopes will more than double the company’s turnover.
The E-Blast sole produced by Aloft weighs around 110 to 120 grams, which compares to the usual 200 grams, but is still more than 80 grams that Chinese producers manage to obtain. Pedro Castro guarantees that safety is a “non-negotiable factor”. “The rules in China still allow the soles to be put in hyperbaric chambers at 300 bar, which is forbidden in Europe. Here, we achieve almost the same performance, but with environmentally friendly and 100% safe manufacturing processes. He emphasises that we don’t compromise on the hygiene and safety of those who work with us”.
Atlanta and its bioplastics
The search for new more ecological and sustainable raw materials is a constant concern for Atlanta, which has several ongoing research products in partnership with organisations in the national scientific system, such as the University of Minho and the Faculty of Engineering at the University of Porto, among others. And bioplastics, soles made from bio-based natural fibres such as cork, sugar cane, coffee grounds or rice husks, among others, are the resulting innovations that were particularly highlighted in Milan.João Carvalho, from Atlanta’s commercial team, explained that the company has managed to develop an 85% plant-based rubber (SBR) in-house, replacing most of the fossil-based materials with plant compounds. Along with recycled and biodegradable materials, bioplastics reinforce Atlanta’s commitment to sustainability, a commitment that has been demonstrated over the years, for example, with the installation of 1,500 photovoltaic panels, which already account for more than 50% of the factory’s energy costs and ensure a reduction of more than 360 tonnes of CO2 emissions per year.
Following the construction of a new industrial pavilion that will allow Atlanta to increase its annual production by 20% to 30%, while improving its operational layout to provide better customer service, the Lixa-based company is preparing to double its solar surface area in the next two to three years in order to become self-sufficient. Of the three million pairs of soles it produces each year, 30% are already made from sustainable materials.
Procalçado launches 100% compostable soles
BioCir®flex, the 100% compostable soles developed by Balena in collaboration with For Ever, the components brand of the Procalçado Group, were the latest innovation presented by the Portuguese company in Milan. And Balena’s technicians were on hand at Lineapelle to explain the paradigm shift that this innovation represents. “The soles of traditional shoes pose recycling challenges, often ending up in landfill sites”, explains Balena on its website, adding that BioCir®flex is made of a “robust bioplastic material”, making it “fully compostable and rich in bio-based content”, thus reducing the environmental impact of footwear production.Committed to presenting a wide range of products that guarantee endless possibilities for its customers, For Ever also introduced Infinity Foam technology, which uses “nitrogen injection”, to create “high-performance and lightweight” soles with “infinite recyclability”, as well as 100% natural rubber soles, among other innovations.
Procalçado, which will celebrate its fiftieth anniversary in 2023, started out making soles and has since evolved into a manufacturer of injected footwear, with the Wock brand in the safety segment and the Lemon Jelly brand in the fashion segment. Sustainability is one of the Group’s main concerns, and it aims to achieve carbon neutrality by 2025.
Vapesol manufactures zero-waste EVA
Since 2022, Vapesol has had a production unit dedicated exclusively to EVA soles and is now “the world’s first zero-waste company” in this manufacturing process. In Italy, this was one of the major innovations presented to customers as part of the FAIST project, which involves 45 organisations and an estimated total investment of 60 million euros.The project resulted from a partnership with Minho University’s Faculty of Engineering, which showed that it is possible to reverse the expansion of EVA so that it can be reintegrated into new soles. Developed with an Italian plastics company with extensive experience in the circular economy, the process has been certified and patented under the EvaPowder brand. It allows up to 20% of EVA waste to be recycled, which is more than the 11% waste that Vapesol’s normal production generates. Décio Pereira, CEO of the Felgueiras company, guarantees that it is currently “the first and only company in the world to have zero EVA waste”.
As a supplier of soles to major luxury brands, Vapesol believes that the recyclability of EVA made possible by the new technology will appeal to its customers, all of whom are increasingly looking to launch new lines of sustainable products. And with this investment, Vapesol is no longer sending 50 tonnes of waste to landfill, for which it paid around 200,000 euros. “Rubbish is the new luxury”, argues Décio Pereira.
Dias Ruivo presents biodegradable leathers
Another BioShoes4All partner is Dias Ruivo. At Lineapelle, the company presented its biodegradable leathers, tanned without the use of heavy metals such as chromium. Ana Dias, the fourth generation of her family to work in the tanning business, admits that vegetable tanning is still a product with limitations, especially in terms of lightfastness.Turning bovine leather into a fashionable product for shoes, but also for leather goods, clothing and even furniture, is the result of generations of experience and continuous investment in research and development. A business that depends on human consumption, giving new life to the hides of animals slaughtered for the food industry and keeping them out of landfills.
“Skin is always biodegradable, it’s just a matter of time. If you don’t use heavy metals, they biodegrade faster, and that’s what we want. But vegetable tanning has many limitations in terms of colour-fastness to light, so we had to evolve the formula and find a way to remove the heavy metals from the process while maintaining the softness of the leather and the resistance of the colour”, explains Ana Dias.
Dias Ruivo has been working on this project since 2022 and is already seeing results, but there is still a long way to go. The aim is to make these skins lighter. “Although they are light skins, they have an effective weight, and it would be great if we could reduce their density by 30%, even to ensure a wider range of applications”, she adds.
Source and Image Credits: portugueseshoes.pt